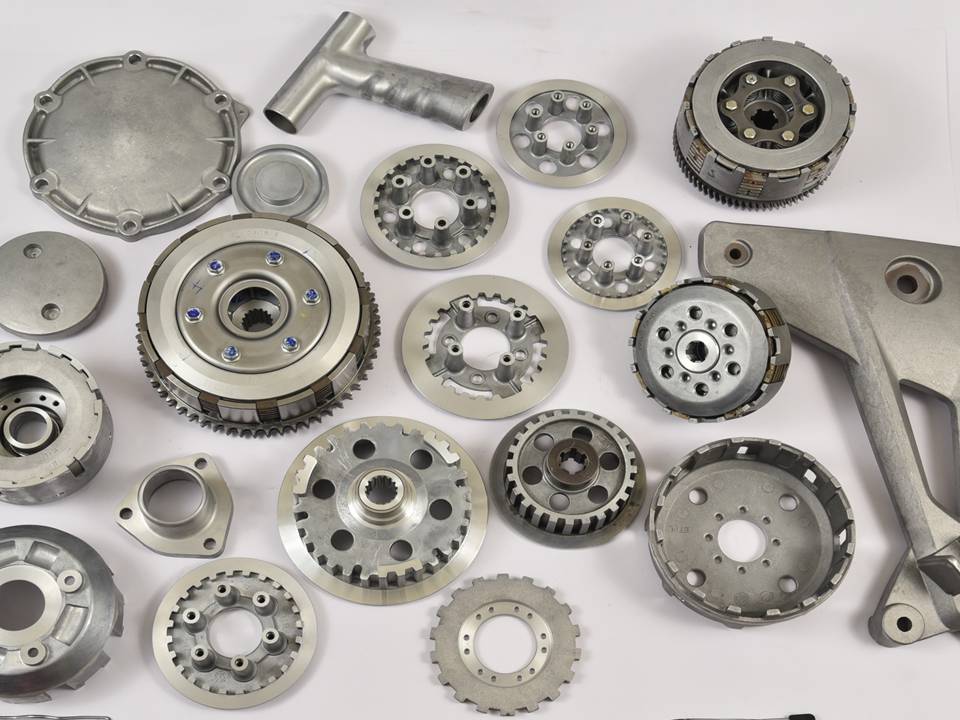
The core of diecasting is the mold, also known as a"die" that is carefully designed and constructed from toughened steel in order to stand up to the tough conditions encountered in diecasting. Die design is essential, because it is required to support the molten metal's flow and hardening while keeping tight tolerances in order to guarantee the highest level of precision. In the process of diecasting, metals such as aluminum, zinc as well as copper are heated until they get molten. The molten metal then gets forced into the die cavity with high pressure, and fills every nook and cranny of the mold. Rapid cooling and formation of solidified metal results in components that have outstanding dimensional precision as well as a polished surface, typically making it unnecessary to perform additional manufacturing or finishing.
One of the most significant advantages of diecasting is its ability to produce mass quantities. When dies are manufactured the dies can then be utilized to create thousands of identical components with the least amount of variation. The high degree of repeatability is crucial for businesses that need large quantities of standardized parts. Additionally, diecasting is known as a material that is efficient. The process generates minimal scrap, because any excess metal is reused in subsequent casting cycles. This not only reduces the cost of material but also promotes sustainable manufacturing practices by minimizing waste and conserving resources. The combination of high productivity, speed of production, and material efficiency makes diecasting a desirable option in the quest to maximize their manufacturing processes.
Diecasting can also provide significant advantages with regard to mechanical properties. The components that are made by diecasting usually offer excellent strength and endurance due to the fine grain structures that are formed from the swift cooling of the molten metal. This makes diecast parts optimal for those applications that require the highest performance and durability. Additionally, it allows to incorporate thin walls and intricate features, without compromising strength and structural strength. This is especially beneficial when it comes to aerospace and automotive industries where weight reduction whilst maintaining strength is vital. Being able to create extremely light and strong components can improve the efficiency of fuel and the performance of vehicles and aircraft. To get extra information kindly check out www.senadiecasting.com.my/
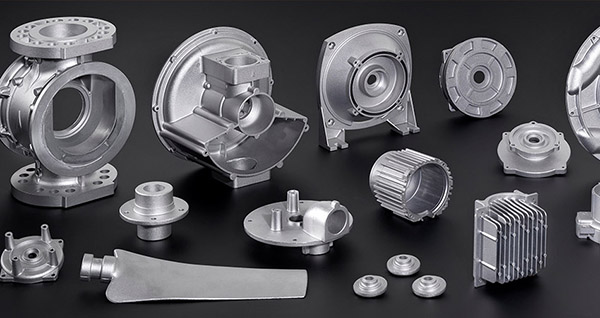
Diecasting's versatility extends to a wide array of applications throughout different industries. Within the automotive sector Diecast components play an integral role in the building of motors, transmissions and structural parts, contributing to the production of lightweight, fuel-efficient cars. In the electronics sector, diecasting is used to make heat sinks connectors, housings, and other components, to ensure optimal thermal management as well as durability for electronic devices. The industry of consumer goods benefits from diecasting, with applications that range from kitchen appliances to power tools, toys and even power tools. The process's adaptability to various metals and its ability to produce parts with intricate patterns make it suitable for numerous uses, all profiting from the distinctive benefits diecasting brings.
Diecasting is an incredibly efficient and versatile manufacturing process that is integral to producing intricate metal components with consistent and high-precision. Its capacity to design parts that have intricate detail with tight tolerances and flawless surface finish makes it indispensable across a range of sectors, from automotive to aerospace, to consumer electronics, and even beyond. Its use of various materials further enhances the versatility of diecasting. It allows companies to choose the most suitable alloy to suit their requirements. Technology advances, and demand for high-quality, cost-effective components continues to grow, diecasting will remain vital on the manufacturing scene driving innovation and excellence when it comes to production.